
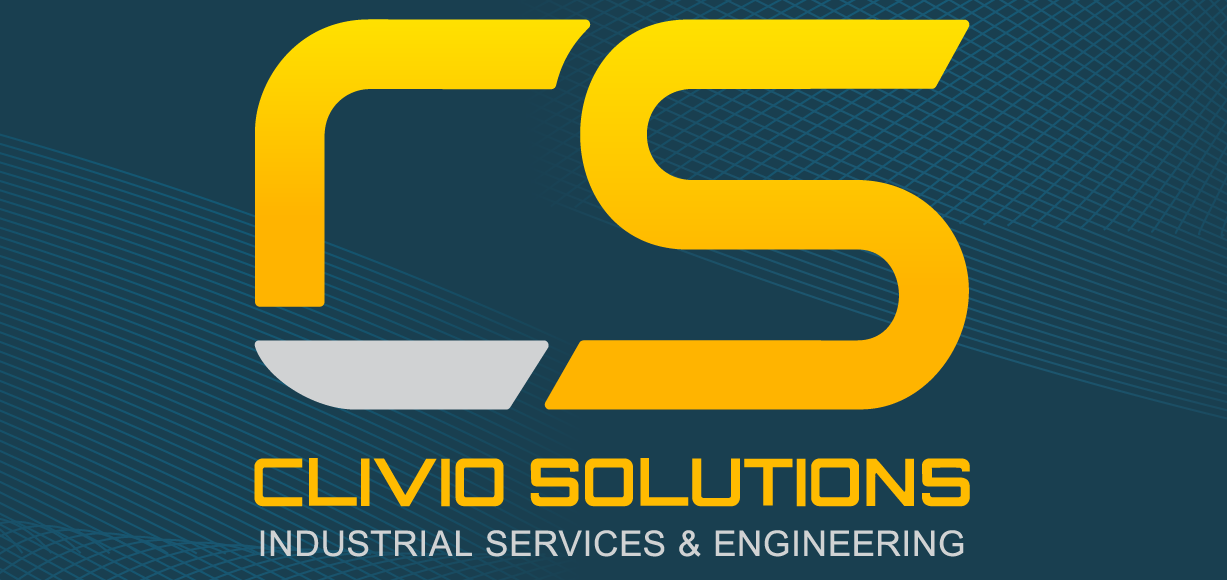
Clivio Solutions
https://www.cliviosolutions.com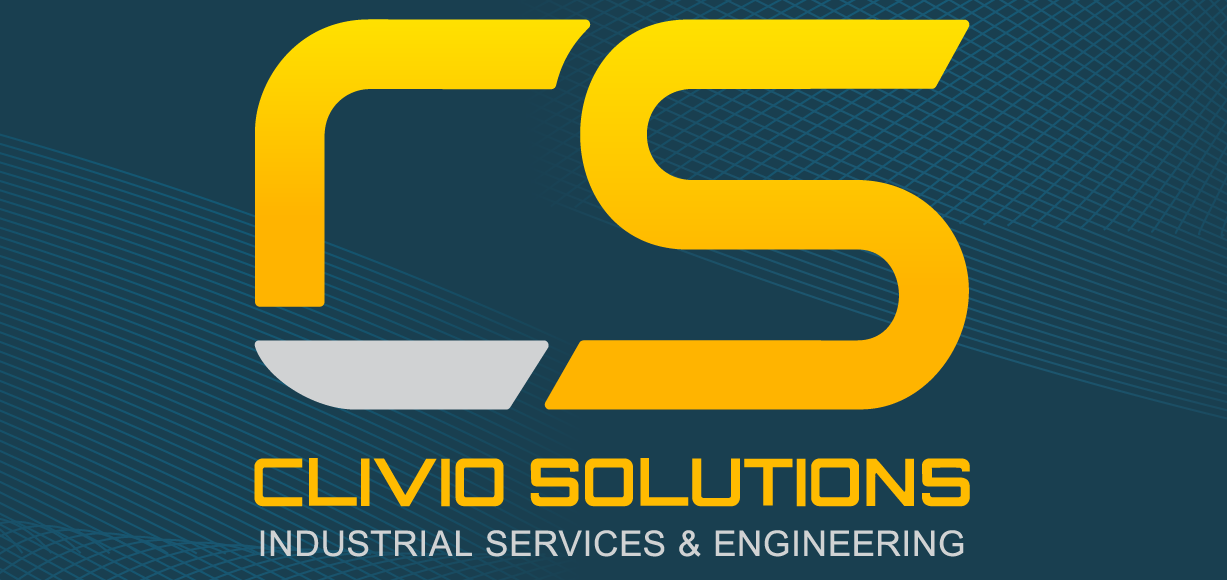
Clivio Solutions
Sobre la empresa
En Clivio Solutions, ofrecemos servicios de ingeniería y consultoría de primer nivel, especializándonos en la industria de alimentos balanceados. Nuestra experiencia se refuerza con asociaciones prestigiosas, asegurando seguridad, adopción de tecnologías de punta y la entrega de soluciones inteligentes y sostenibles. Nuestra propuesta de valor se basa en la integridad, una diversidad de soluciones y un amplio alcance geográfico. Sobresalimos en fomentar la sinergia, actuando como facilitadores dedicados y ofreciendo soporte continuo caracterizado por una fiabilidad y calidad inigualables.
Noticias de la empresa
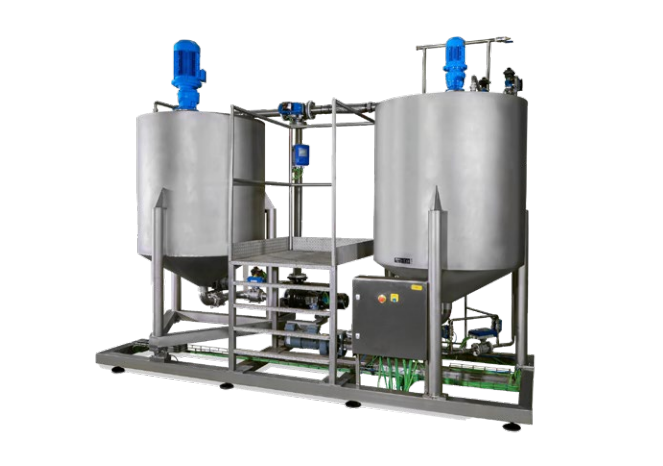

2+ MIN




11/09/2024
Recupero de subproductos en la fabricación de alimentos para mascotas
Desafíos con los subproductos húmedos
Los subproductos húmedos presentan un alto contenido de humedad, lo que los hace difíciles de manejar debido a su rápida descomposición y la generación de microorganismos no deseados que pueden poner en riesgo la salud de las mascotas. Generalmente, estos subproductos se comercializan a bajo valor para la alimentación de animales de granja o se desechan.
Problemas con los finos de proceso
Los finos suelen reinsertarse de manera ineficiente en el proceso de molienda o mezclado, lo que conlleva varios problemas:
Moler un producto que ya fue molido.
Consumir energía adicional en la molienda.
Desgaste en martillos y cribas del molino.
Afectar la capacidad de los equipos que reprocesan estos subproductos.
Solución sostenible: Sistema de Recupero de Subproductos (SRS)
El Sistema de Recupero de Subproductos (SRS) es una solución comprobada para reducir, reutilizar y reciclar tanto los subproductos húmedos como los secos, sin importar su tamaño, temperatura y contenido de humedad.
Componentes del SRS
El SRS cuenta con dos tanques:
Tanque de homogenización: recibe los subproductos a recuperar. Posee una cuchilla de diseño especial que gira a alta velocidad para lograr una mezcla homogénea (slurry) con una concentración aproximada de 20% de subproductos y 80% de agua a una temperatura de entre 40 y 50 °C.
Tanque de mantenimiento: una vez lograda la mezcla homogénea, se transfiere a este tanque mediante tuberías. Aquí, un mezclador mantiene el slurry homogéneo y con la viscosidad adecuada.
El sistema de control del SRS se comunica con el PLC del preacondicionador-extrusor para asegurar el contenido correcto de agua dentro del preacondicionador y extrusor, evitando variaciones no deseadas en el contenido de humedad y garantizando la calidad óptima y uniformidad del producto final.
Ventajas del SRS
Recupero de la inversión en poco tiempo.
Aprovechamiento inmediato de todos los subproductos, evitando la generación de microorganismos no deseados.
Optimización de los tiempos de proceso.
Disminución de los requerimientos de mano de obra.
Mejora en la trazabilidad.
Logro de la automatización.
Cumplimiento con las certificaciones FDA y EHEDG.
Fabricado en acero inoxidable.
Adaptable a espacios en planta mediante disposición horizontal o vertical.
Dimensionamiento del SRS
Para dimensionar el SRS adecuado para tu proceso, es necesario determinar la cantidad de subproductos generados. Con esta información, se puede seleccionar el modelo adecuado. Existen tres modelos estándar: SRS150, SRS300 y SRS600, que recuperan 150, 300 y 600 kg/h respectivamente. También se pueden diseñar soluciones especiales según las necesidades específicas.
Por: Clivio Solutions
Fuente: All Pet Food Magazine
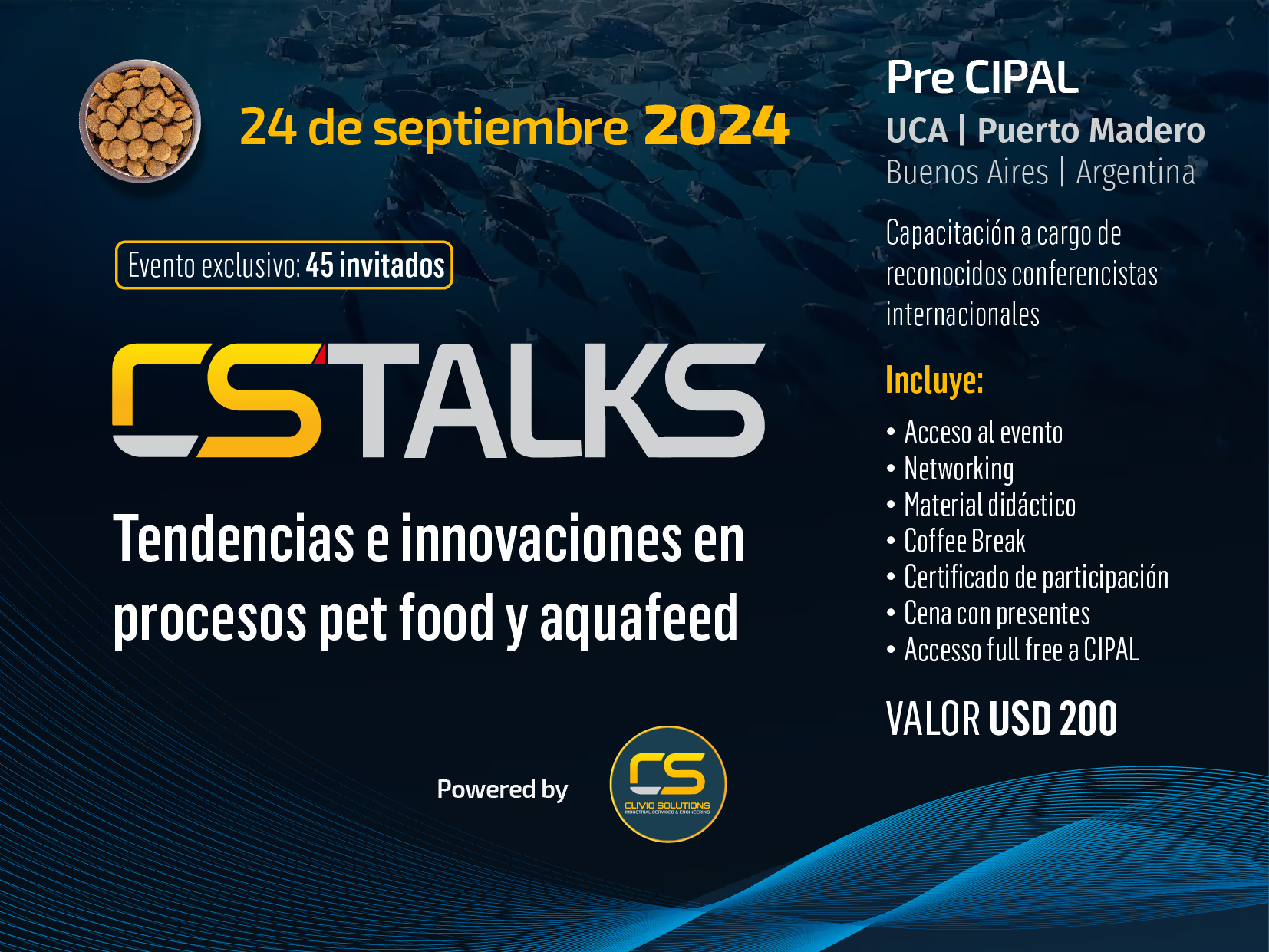

2+ MIN
19/08/2024
CS Talks 2024: Un encuentro exclusivo para los líderes de la industria pet food y aquafeed
Nos enorgullece contarte que creamos nuestro propio evento, CS Talks, impulsado por Clivio Solutions, y queremos invitarte a ti y a tu equipo a ser parte. Es un evento exclusivo y una jornada única, diseñada para ofrecerte una experiencia inolvidable. Haciendo sinergia con CIPAL, CS Talks 2024 tendrá lugar el 24 de septiembre de 2024, día previo a CIPAL, desde las 14:00 hs hasta las 20:00 hs en la Universidad Católica Argentina, ubicada en Puerto Madero, Buenos Aires, Argentina. En línea con el tópico del evento denominado 'Tendencias e innovaciones en procesos pet food y aquafeed', se desarrollarán diferentes capacitaciones llevadas a cabo por reconocidos profesionales y conferencistas internacionales de la industria. ¡Observa la imagen para conocer el programa completo! ¿Te interesa ser parte? Ponte en contacto con nosotros haciando CLICK AQUÍ para verificar disponibilidad de espacios ¡Quedan pocos lugares! SOBRE LA EMPRESA En Clivio Solutions, ofrecemos servicios de ingeniería y consultoría de primer nivel, especializándonos en la industria de alimentos balanceados. Nuestra experiencia se refuerza con asociaciones prestigiosas, asegurando seguridad, adopción de tecnologías de punta y la entrega de soluciones inteligentes y sostenibles. Nuestra propuesta de valor se basa en la integridad, una diversidad de soluciones y un amplio alcance geográfico. Sobresalimos en fomentar la sinergia, actuando como facilitadores dedicados y ofreciendo soporte continuo caracterizado por una fiabilidad y calidad inigualables. Fuente: Clivio Solutions
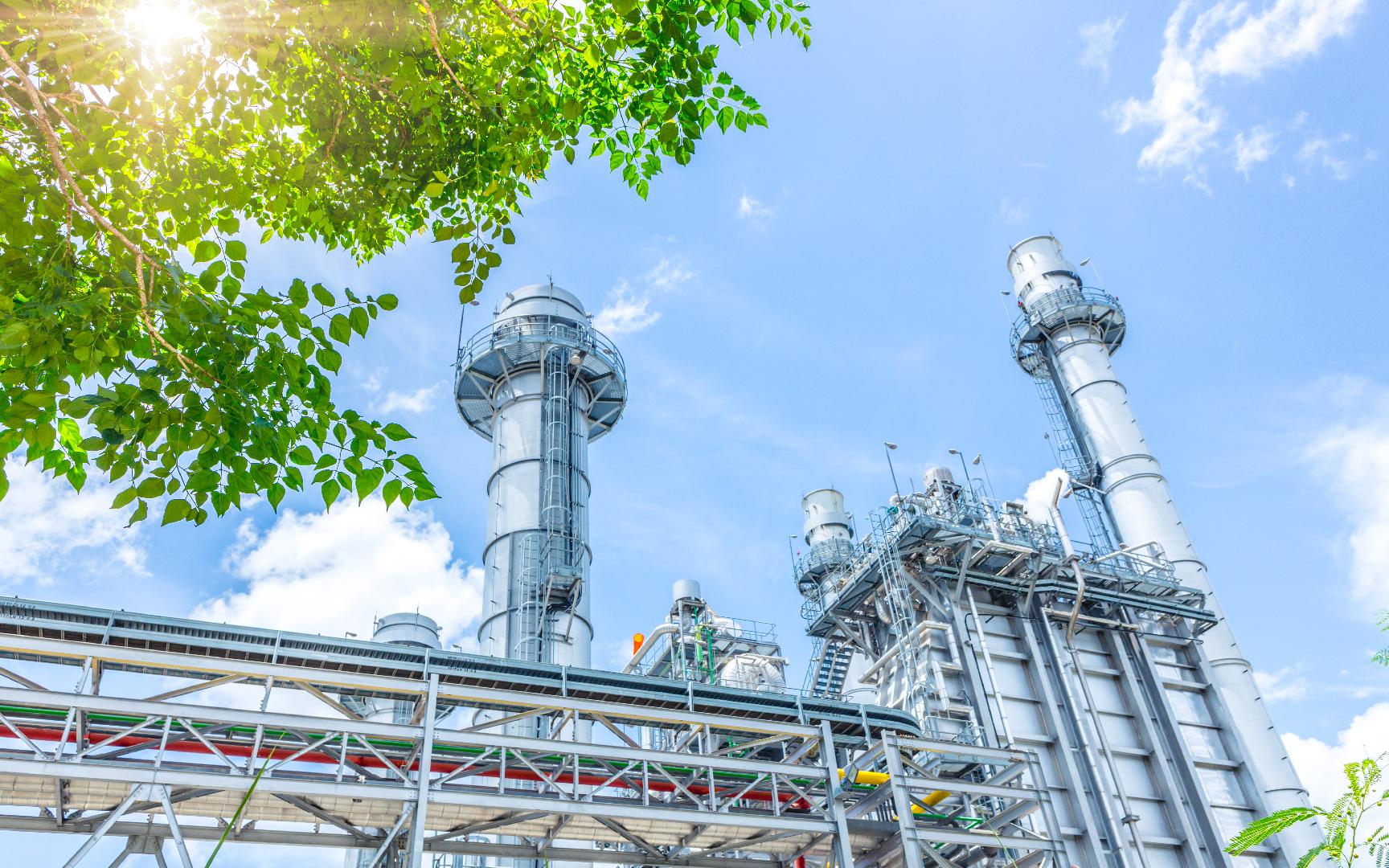

4+ MIN
23/02/2024
Comparación de tecnologías de control de olores
Tecnología de Biofiltro
El aire de proceso que contiene el olor molesto es tratado mediante un material filtrante, normalmente, pellets de madera, y eliminado por microorganismos situados en el mismo, y puede reducir diversos compuestos como sulfuros, amoniacos y aminas, cuando se presentan en bajas concentraciones. Luego, el aire limpio es emanado a la atmósfera, quedando como contaminante el drenaje residual (nitratos y sulfuros) que necesariamente debe ser tratado debido a que, en caso contrario, continúan causando malos olores.
Este sistema puede tratar caudales de 1,000 a 50,000 m3/h, requiere de agua para su funcionamiento y de una gran área para su implementación, utilizando poca energía eléctrica.
Para evitar dañar el material filtrante, se debe considerar llevar a cabo un mantenimiento periódico. Cuando se trata de aire de proceso con alto contenido de polvos, es obligatorio y necesario tratarlos, por ejemplo, mediante un lavador de gases.
Es considerada como una buena tecnología por su relación costo/eficiencia, obteniendo resultados que alcanzan el 85% de olores eliminados. En cuanto a los costos de inversión, a pesar de que pueden variar por marca, fabricante o modelo, generalmente, oscilan entre los USD 700,000 y USD 1,000,000.
Tecnología de Tratamiento de ozono y luz UV
El flujo de aire, el cual debe ser menor a 20,000 m3/h, atraviesa en primer lugar las luces UV donde se descomponen los amoniacos, sulfuros y aminas, para luego descomponer los compuestos restantes con catalizadores mediante la inyección de ozono (O3).
Es importante eliminar el polvo del aire del proceso ya que dañarían la efectividad de la luz UV. Es decir, un aire muy contaminado puede afectar considerablemente la eficiencia del sistema debido a la densidad del flujo.
Por otra parte, utiliza energía eléctrica para su funcionamiento y el aire no debe superar los 60°C, ni la humedad debe ser mayor a 85%.
Este tratamiento permite lograr buenos resultados, alcanzando niveles de 70 a 90%. Respecto de los costos de inversión, se consideran entre USD 200,000 y USD 400,000, con altos costos operativos anuales.
Tecnología de Plasma no térmico (NTP)
Tecnología capaz de tratar caudales que van desde los 5,000 m3/h hasta los 200,000 m3/h, dependiendo del tipo de sistema: en el caso de NTP directo normalmente 20,000 m3/h son tratados, pero para el caso de la tecnología NTP indirecta se pueden tratar hasta 250,000 m3/h. Estos equipos utilizan aire ambiente para generar oxígenos libres o activos (O1), los cuales tienen un alto poder de oxidación con las moléculas que contienen el olor molesto. Con el fin de obtener los oxígenos activos, el aire debe pasar a través de una etapa de filtros para librarlos de impurezas y luego atraviesa el gabinete con módulos de plasma no térmico, donde se logra la disociación de las moléculas y se obtiene los radicales de oxígeno. Éstos, son inyectados en el ducto de salida de donde provienen los olores molestos y en apenas 1 segundo las moléculas olorosas reaccionan y se oxidan, transformándose en imperceptibles para nuestra nariz.
A diferencia de otras tecnologías, el plasma no térmico no utiliza agua ni químicos para su funcionamiento por lo que no genera un subproducto contaminado secundario, solo requiere un mínimo de energía eléctrica. Además de los grandes caudales que puede tratar, no existe una restricción hacia la humedad ni temperatura que los aires de procesos pueden tener.
Se logran óptimos resultados, alcanzando niveles de hasta 95% de olores eliminados.
Son sistemas que se adaptan fácilmente a instalaciones existentes, gracias a la flexibilidad y poco espacio que ocupan. Con respecto a los niveles de inversión, estos van desde los EUR 120,000 hasta los EUR 250,000.
Tecnología de Scrubber
El aire proveniente del proceso, el cual contiene el olor molesto, entra en contacto con la corriente de agua y químicos tipo lluvia por goteo y, de esta manera, los olores reaccionan o son disueltos en el líquido y el aire es emanado a la atmósfera de forma limpia.
Los scrubbers, también conocidos como lavadores de gases, pueden tratar flujos de aire que contengan polvos, sin la necesidad de utilizar filtros. Pueden tratar flujos que van desde los 1,000 hasta 60,000 m3/h, logrando buenos resultados desde un 50% hasta un 70% de los olores controlados.
Una gran desventaja que tienen es que se requiere de un control estricto de las aguas contaminadas que se generan luego del proceso, además ocupa un área grande para su instalación.
La inversión puede alcanzar hasta USD 500,000 con los costos operativos altos cercanos a los 150,000 USD al año.
Conclusión
A modo de resumen, véase un cuadro comparativo de las tecnologías presentadas con sus ventajas y desventajas, considerando como puntuación lo siguiente: 5 altamente positivo, 4 positivo, 3 medio, 2 negativo y 1 altamente negativo.
La elección e instalación del sistema adecuado va a depender, por un lado, del proceso industrial que se requiera tratar considerando los componentes del aire contaminado y, por otro, de los niveles de control de olores que se deban lograr para cumplir con las normativas vigentes de cada país.
Por: Clivio Solutions.
Fuente: All Pet Food Magazine.
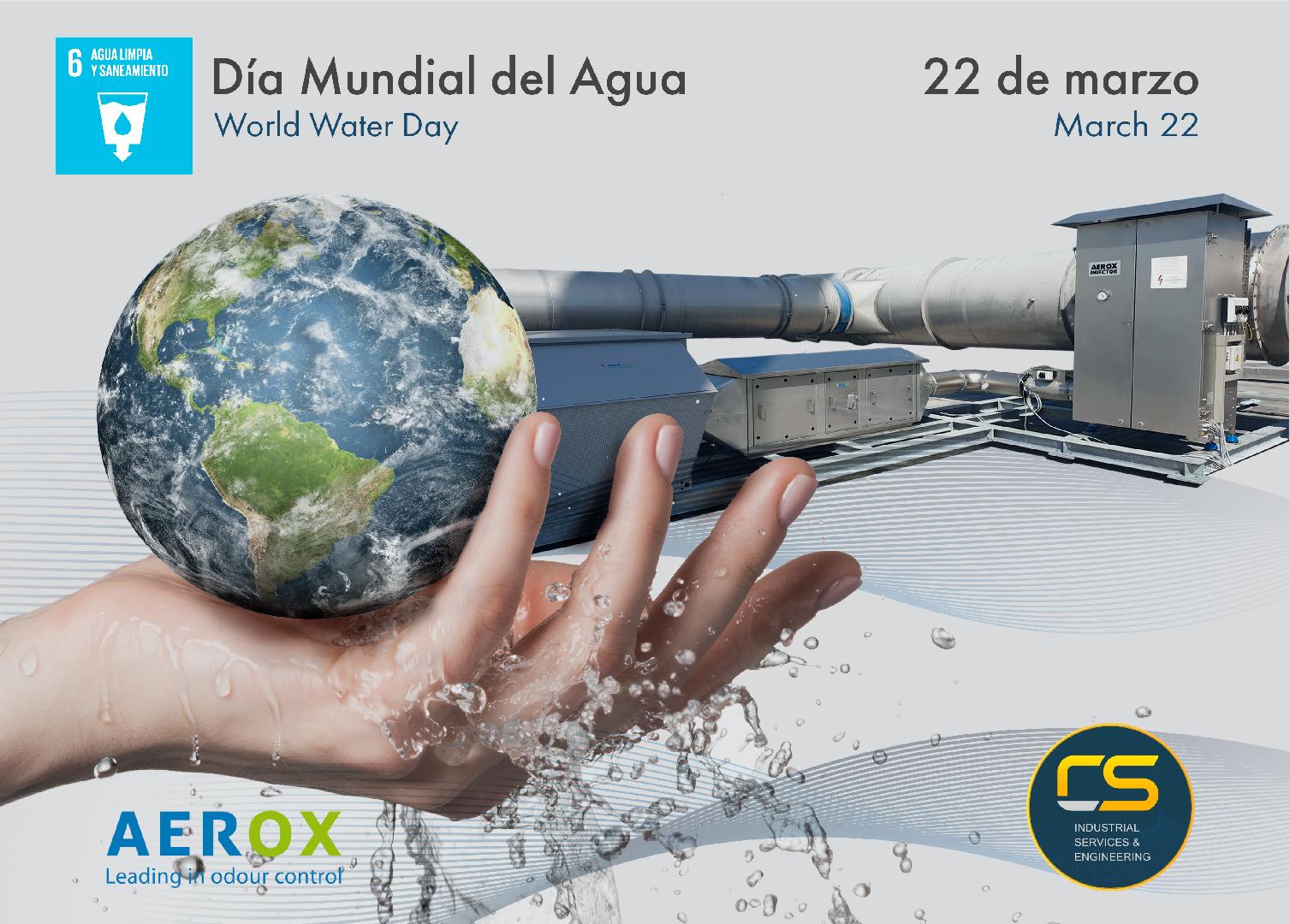

4+ MIN
22/03/2023
Día Mundial del Agua
Este día se celebra bajo el lema 'Aguas subterráneas: Hacer visible el recurso invisible', por la UNESCO, la agencia líder de la ONU. En 2015, el mundo se comprometió con el 6.° Objetivo de Desarrollo Sostenible (ODS) como parte de la Agenda 2030: la promesa de que todos tendrían agua y saneamiento gestionados de forma segura. Este año la celebración de este día mundial coincide con el arranque de la Conferencia de la ONU sobre el Agua 2023 (22-24 de marzo, Nueva York). Ésta será una oportunidad única para buscar soluciones a la crisis actual. Miles de millones de personas e innumerables escuelas, empresas, centros de salud, granjas y fábricas se ven restringidas porque aún no se han cumplido sus derechos humanos de acceso al agua y a su saneamiento. Hoy en día, nos encontramos muy lejos de conseguirlo. Por tal motivo, desde la industria pet food entendemos la seriedad de la problemática y asumimos la responsabilidad de cuidar este bien natural no renovable, como una forma de valoración constante a un recurso que nos permite producir alimentos, mejorar la calidad de vida de las mascotas y así ver crecer a una industria en pleno auge. Somos conscientes de que tenemos al alcance de nuestras manos, un recurso que aún hoy, no está disponible para toda la población mundial. Y estamos también convencidos de que existen medidas rápidas y transformadoras entre las cuales puede estar incluida la acción individual de cada uno de nosotros. Es por eso que hoy, te contamos sobre la interesante Tecnología de Plasma No Térmico - NTP- del Aerox Injector, que contribuye con el cuidado de dos recursos: el aire y el agua. Actualmente, la emisión de olores a la atmósfera por los procesos industriales es también preocupante y está siendo cada vez más regulada por las autoridades gubernamentales y los entes que trabajan para minimizar el impacto de la contaminación de nuestro planeta. El sistema Aerox Injector es reconocido mundialmente como 'La mejor tecnología disponible' para el control de los olores que se generan durante el proceso de fabricación de alimentos para mascotas, sin la utilización de agua. Entre sus principales ventajas, y a diferencia de otras tecnologías, se destaca la no utilización de agua para su funcionamiento. Por lo tanto, además de no provocar contaminación odorífica, y el consumo de un recurso no renovable como el agua, tampoco genera el desecho (verter) de efluentes líquidos contaminados al medioambiente, por lo que no es necesario tratar un efluente contaminante secundario. ¿Cómo es el funcionamiento del sistema? El Aerox Injector es una unidad de plasma no térmico situada en el exterior del conducto de salida de aire de proceso que con un ventilador toma aire ambiente haciéndolo pasar por un filtro de tres etapas y por un pequeño calentador para liberar el aire de partículas. Posterior al proceso de purificado este aire atraviesa los módulos NTP, donde con un mínimo de electricidad se generan los radicales de oxígeno libre. Estos radicales son entonces inyectados en el ducto de aire de escape del proceso reaccionando con las moléculas que tienen el mal olor, oxidándolas y transformándolas en inodoras e inofensivas para los vecinos y medio ambiente. La reacción se produce de manera instantánea en menos de 1 segundo. Imagen 1 Adicionalmente, podemos mencionar que logra niveles de reducción de olores de hasta un 95%, y tiene un tamaño compacto haciéndolo muy adaptable a las instalaciones. Además, de ser posible, se pueden tratar con un único Aerox Injector los aires de salida de proceso combinando los ductos (ver imagen 1). De esta manera, hoy podemos confirmar que la tecnología y las soluciones aplicadas a la industria pet food, persiguen el desafío constante de minimizar el impacto en sus procesos productivos. Los invitamos a visitar los sitios web de CLIVIO SOLUTIONS y AEROX. Fuente: Clivio Solutions
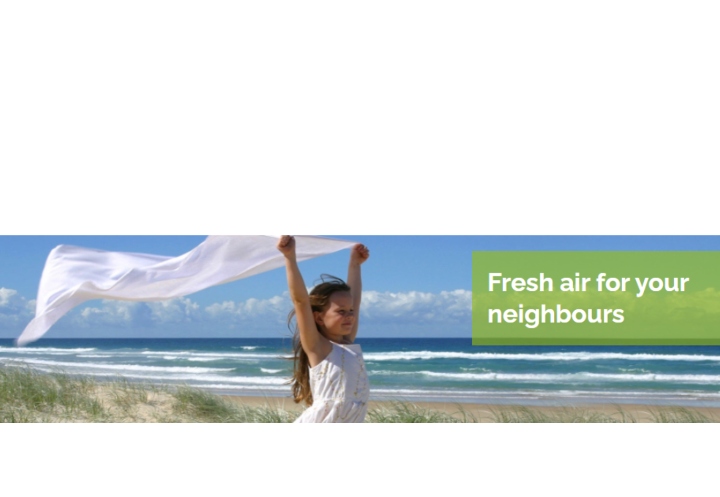

5+ MIN
30/09/2020
¡Controle la emisión de Malos Olores en Plantas de Alimentos para Mascotas!
AEROX suministra soluciones de control total de olores a largo plazo para Industrias de todo el mundo. Ayudamos a nuestros clientes a reducir sus emisiones para cumplir con la legislaciones industriales y gubernamentales.
El Aerox®-Injector elimina los malos olores producidos en procesos industriales y es reconocido por gobiernos y compañías del sector como `Mejor Tecnología Disponible´.
Una reducción de malos olores de hasta el 95 % y una técnica única para eliminar olores de procesos de aire húmedo, han supuesto una elección fácil para múltiples líderes de mercados mundiales.
UN DEDICADO ENFOQUE MEDIOAMBIENTAL
Dado que el mal olor es más una molestia que un asunto político o un problema medioambiental, se encuentra entre las prioridades de compañías de todos los sectores. La imagen corporativa y la responsabilidad social son esenciales para el estatus y el éxito de compañías hoy en día, los responsables están dispuestos a invertir en tecnologías para combatir dichas molestias.
El Aerox®-Injector está diseñado específicamente considerando el medio ambiente. El inyector no requiere agua, productos químicos o combustible para operar.
Gracias a su tecnología única de oxígeno activo, que se basa en el principio de pasar aire entre cátodos y ánodos especialmente preparados, todo lo que requiere es una cantidad relativamente pequeña de electricidad. Además el programa de Servicio de Aerox garantiza que todos los consumibles son completamente reciclados: respetuoso con el medio ambiente.
DE ELECTRICIDAD A AIRE LIMPIO
- Sin combustible
- Sin gas
- Sin agua
- Sin productos químicos
- Sin residuos
LÍDER EN CONTROL DE MALOS OLORES
El objetivo principal de nuestros esfuerzos es eliminar los malos olores resultantes de sus procesos de producción a nivel de tierra. La base de nuestra tecnología es el Aerox®-Injector, una pequeña unidad fijada al exterior del conducto de salida de los gases de proceso que inyecta 'oxígeno activo' en él. Oxida las moléculas malolientes, convirtiéndolas en imperceptibles al olfato humano.
Así, por medio del Aerox®-Injector, sus vecinos disfrutarán de algo incuestionable: AIRE LIMPIO. Aerox dispone de la experiencia y el saber de las fuentes y las composiciones de los malos olores de muchas Industrias así como el conocimiento de sus respectivos procesos de producción. Esto permite una minuciosa determinación de la complejidad de cada situación específica y la mejor solución posible. Aerox reducirá las emisiones de malos olores de su planta a niveles aceptables y a menudo, incluso, eliminarlos simultáneamente.
EL AEROX®-INJECTOR , TECNOLOGIA DE PLASMA NO TERMICO
El Aerox®-Injector es una unidad de plasma no térmico situada en el exterior del conducto de gas de proceso. Se utiliza aire ambiente limpio para generar los radicales de oxígeno, que son inyectados en el caudal de aire de salida, oxidando las moléculas de mal olor presentes y por lo tanto, convirtiéndolas en inofensivas.
VENTAJAS DE UN VISTAZO
- Control de malos olores sumamente efectivo
- Inyección permite tratar grandes volúmenes de aire de proceso
- Bajo costo de propiedad
- Sin necesidad de agua, gas, ni productos químicos. Sin residuos.
- Mejor Tecnología Disponible (B.A.T.)
CONTROL DE MALOS OLORES EN DIVERSAS INDUSTRIAS
Aerox, inventor de la tecnología de control de malos olores mediante inyección de plasma no térmico, posee una demostrada experiencia de 25 años en control de malos olores en múltiples sectores de la industria. La lista de industrias específicas continúa en aumento.
Las soluciones de control de olores realmente duraderas requieren tecnología avanzada y hecha a medida. La mejor manera de controlar los malos olores es el estudio de cada caso específico. Obviamente, el punto de partida de cualquier solución que Aerox suministra son el origen del proceso de producción y los malos olores resultantes de éste.
Otros factores como el clima, la situación geográfica y legislaciones gubernamentales son estudiadas in situ en cada caso concreto.
Además, cada unidad Aerox®-Injector es ajustada durante la puesta en marcha por un ingeniero debidamente cualificado de Aerox.
Líderes de mercados mundiales eligen Aerox
Aerox B.V. es el líder mundial en control de malos olores por medio de la tecnología eficiente y respetuosa con el medio ambiente de inyección de plasma no térmico. Poseemos profundo conocimiento y experiencia en todos los aspectos de los procesos de control de olores, en diversas industrias.
El proceso de Aerox comienza reuniendo información y proporcionando consejo sobre la viabilidad de contratar Aerox en su caso específico. Nuestro consejo se basa en la información que usted nos proporcione por teléfono o mediante cuestionario, así como los detalles de su proceso industrial, volúmenes de aire, la localización geográfica y condiciones climatológicas.
Los problemas de malos olores son complejos y únicos. Aerox, por lo tanto, ofrece ensayos in situ en fábrica permitiendo a sus clientes determinar qué rendimiento y en qué capacidad de Aerox. En base a los resultados obtenidos del ensayo Aerox diseña y ofrece soluciones óptimas de control de malos olores. Un equipo experimentado y debidamente cualificado de ingenieros de proyecto de Aerox cooperarán con ingenieros del cliente para garantizar un óptimo proceso de implementación, hecho a medida para las condiciones y
requisitos de la planta. Tras la puesta en marcha Aerox se centrará en una cooperación a largo plazo para ofrecer servicio de mantenimiento tales como reemplazo de los módulos y control remoto. Esto permite reducir los costos de mantenimiento y el buen funcionamiento del Aerox®-Injector.
MÁS INFORMACIÓN
Si desea más información sobre el Aerox®-Injector, o recibir una propuesta para su planta o saber más de control de malos olores en general, mande por favor un e-mail a [email protected] o llame directamente al teléfono +54 9 236 4418899.
Si quiere saber más del funcionamiento puede ver video en español:
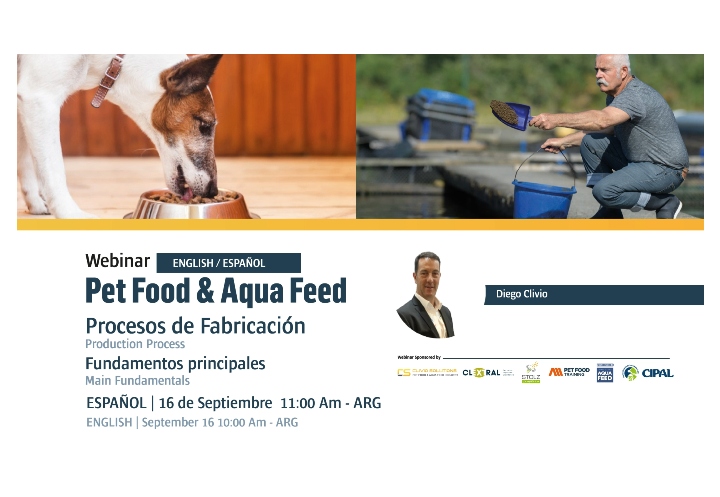

1+ MIN
29/09/2020
¿Quieres ver el Video completo del Webinar de Proceso de Elaboración de Pet Food & Aqua Feed?
Video corto promocional: Solicite el Video Completo por email a: [email protected] Estadísticas de registrados el pasado 16-Sept-2020:
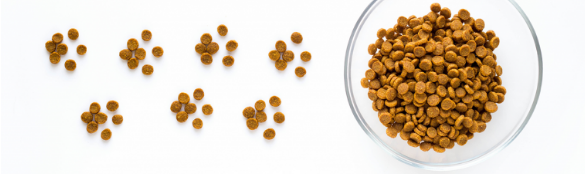

5+ MIN
04/06/2020
Sistemas de Extrusión para Pet Food y Aqua Feed. ¿Simple o Doble tornillo?
El proceso de Extrusión es un proceso termo-mecánico que consiste en forzar un producto a pasar por uno o varios orificios de un tamaño específico bajo presión y temperatura gracias al concepto del tornillo de Arquímedes (también conocido como 'tornillo sin fin'). Los procesos de extrusión en la elaboración de alimentos extrusados para mascotas y acuicultura, tienen como objetivo lograr la cocción de la mezcla de materias primas e ingredientes dándole forma de croqueta (pellet / kibble) que facilita su posterior manipulación. Lo más importante que acontece dentro de los extrusores es la gelatinización de almidones y texturización de proteínas, ambos procesos ayudan a la mayor digestibilidad, como así también a formar una estructura y textura que aloje otros ingredientes, minerales, grasas de manera estable y uniforme. Para una buena gelatinización de almidones y texturización de proteínas se necesita humedad (la que se adiciona en forma de agua líquida y vapor en pre acondicionador y/o extrusor), se necesita temperatura, una parte del aporte de temperatura se da por el agregado de vapor, pero la más importante se lleva a cabo por el trabajo mecánico y de rozamiento que producen los tornillos y se necesita también energía mecánica, otorgada por la acción de cizallamiento de los tornillos. Hoy existentes dos tecnologías disponibles para extrusión, estas son simple tornillo (SSE) y doble tornillo (TSE). En este artículo hablaremos de las características, ventajas y desventajas de cada una de estas tecnologías. Extrusores Simple Tornillo En los Extrusores de Tornillo Simple observamos como característica que el avance del tornillo mueve los materiales a través del canal al desarrollar un 'flujo de arrastre', cuya velocidad es directamente proporcional a la velocidad del tornillo. Debido a la restricción de la matriz en la descarga del extrusor, existe un 'flujo de contrapresión', que va en dirección opuesta al flujo de arrastre. Por lo tanto, la 'tasa de flujo' en extrusores simple tornillo (SSE) equivale a la tasa de flujo de arrastre – tasa de flujo de contrapresión. La dinámica de flujo en el canal del tornillo nos muestra que las partículas de fluido viajan a distintas velocidades y que no interactúan en su totalidad, lo que resulta en una dispersión de los tiempos de permanencia y una mezcla poco uniforme. En consecuencia, la transferencia de calor, así como la entrega de energía mecánica en la sección de cocción son muy limitadas. Además, la extensión del cizallamiento depende del espacio, lo que genera heterogeneidades de las propiedades de fusión (duración de la cocción, temperatura y presión). En resumen, tecnología simple tornillo (SSE) presenta: Una única sección de proceso. Dependencia del rendimiento y velocidad del tornillo. Un único punto operativo (rendimiento combinado con la máxima velocidad del tornillo y área de apertura de la matriz). Limitaciones en mezclado, lo que limita la transferencia de calor, entrada de energía mecánica, y genera heterogeneidades en la fusión de partículas (duración de la cocción, composición, temperatura y presión). A mayor desgaste del tornillo, menor rendimiento del extrusor. Se puede observar una reducción de 10-20% durante la vida útil del tornillo. 'Factores de lubrificación' en la composición de la mezcla generan escurrimiento, el cual reduce el rendimiento del extrusor y la adición de energía mecánica. Extrusores Doble Tornillo Los Extrusores Doble Tornillos corrotantes (TSE) tienen múltiples secciones de proceso en serie, (fusión/cocción, extracción de vapores/gases, bombeo de desplazamiento positivo), gracias a las distintas restricciones generadas por el trabajo de los tornillos. Las secciones de proceso muestran altos niveles de mezcla, buena transferencia de calor e importante trabajo de cizallamiento (adición de energía mecánica). En los TSE corrotativos, se observa una mezcla muy intensa en la zona de acople de los tornillos (macro mezcla y micro mezcla). En consecuencia, el coeficiente de transferencia de calor en las secciones es muy alto. Se pueden obtener fusiones homogéneas, con una muy buena ligazón de lípidos. La expansión tras atravesar la matriz se desarrolla consistentemente, lo que lleva a dar una excelente densidad, textura y forma del producto, así como también una densidad y color final uniforme. En resumen, la tecnología doble tornillo (TSE) presenta: Múltiples secciones de proceso en serie. El rendimiento y la velocidad del tornillo están desvinculadas. Por lo tanto, para una mezcla formulada, los TSE corrotativos se caracterizan por sus múltiples puntos operativos. Además, el perfil del tornillo puede variar extensivamente para modular la adición de energía mecánica. El proceso de mezclado es muy intenso, lo que da grandes beneficios en relación con la calidad del producto. El deslizamiento de la mezcla es compensado por el bombeo de desplazamiento positivo de los tornillos. Menor sensibilidad a cambios de materias primas. Mayor tolerancia a cambios de humedad, agregados de fibras y grasas. Mejor calidad y consistencia de producto final. Mayor flexibilidad general del proceso. En Aqua Feed la mejor uniformidad y alto nivel de desgasificado posible disminuye las chances de que haya pellets que floten cuando se producen alimentos hundibles. En Aqua Feed nos permite llegar a producir, gracias a la acción de los dos tornillos, micro pellets de hasta 500 micrones (0,5 mm). En el caso particular de los Extrusores Doble Tornillos de la Empresa Francesa 'Clextral' (imagen superior de extrusor Clextral), se logra adicionalmente la ventaja probada de poder lograr la elevada calidad de alimentos trabajando con 2 a 3 % menos de humedad, lo que implica importantes ahorros en energía en el proceso posterior de Secado. Conclusión Ambas tecnologías de extrusión son ampliamente utilizadas en el sector de la elaboración de Pet Food y Aqua Feed. La tecnología de Simple Tornillo exige normalmente un costo de inversión menor, y de alguna manera menores costos de repuestos. Mientras que la de Doble Tornillos requiere una inversión superior que trae como ventajas la posibilidad de trabajar con un abanico de materias primas mayor, con más fibras, más proteínas vegetales y mayor contenido graso. Autor: Ing. Diego Clivio Más info: www.cliviosolutions.com
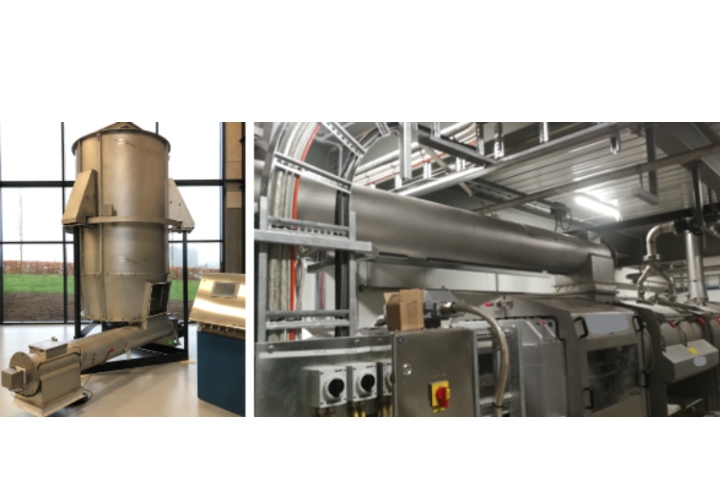

1+ MIN
21/05/2020
Control exacto del flujo de producto que ingresa al Extrusor
Me permito hacer una presentación de los equipos de LIW 'Loss In Weight' de la prestigiosa Empresa JESMA para medición del flujo de producto que entra al acondicionador/extrusora. Como Uds. conocen, el buen funcionamiento de estos equipos asegura una alimentación gradual y exacta del material que entra al acondicionador y así a la extrusora. Si este equipo no opera adecuadamente la calidad del producto final puede verse muy comprometida ya que las variaciones de densidad y las fluctuaciones en esta área son muy frecuentes. Variaciones en la alimentación y lecturas erróneas del flujo de producto que ingresa provocan adiciones erróneas de vapor y agua produciendo variaciones en las condiciones de trabajo de la extrusora (SME – Specific Mechanical Energy). Un sistema preciso y confiable de medición del flujo de producto que llega al acondicionador permitirá un agregado de agua y vapor en las proporciones adecuadas y por lo tanto un proceso continuo de mayor calidad, sin depender tanto de los ajustes intuitivos de los operadores. Ver presentación Fuente: www.cliviosolutions.com